1. |
Check the crankshaft main bearing oil clearance.
(1) |
To check main bearing - to - journal oil clearance, remove the
bearing caps with their lower bearings.
|
(2) |
Clean each main journal and lower bearing with a clean shop towel.
|
(3) |
Place one strip of plastigage across each main journal.
|
(4) |
Reinstall the bearing caps with their lower bearings, then tighten
the bolts.
Tightening torque :
17.7 - 21.6 N·m (1.8 - 2.2 kgf·m, 13.0 - 15.9 lb·ft)
+ 88 - 92°
|
• |
Always use new crankshaft main bearing cap bolts.
Crankshaft main bearing cap bolts are toque - to
- yield bolts designed to be permanently elongated
beyond the state of elasticity when torqued, so
if the bolts are removed and reused, it may cause
the bolts to break or fail to maintain clamping
force.
|
• |
Do not turn the crankshaft.
|
|
|
(5) |
Remove the bearing caps with their lower bearing again, and measure
the widest part of the plastigage.
Oil clearance
No.1, 2, 3, 4, 5 : 0.020 - 0.041 mm (0.0008 - 0.0016
in)
|
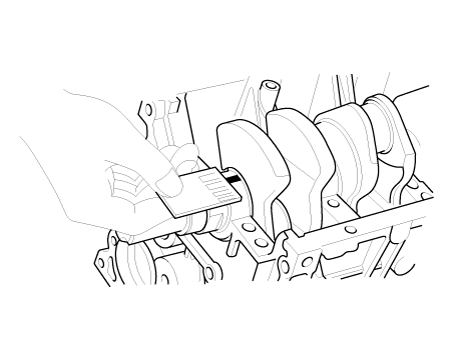
|
(6) |
If the plastigage measures too wide or too narrow, remove the
upper and lower bearing and then install a new bearings with the
same color mark. Recheck the oil clearance.
Do not file, shim, or scrape the bearings or the caps
to adjust clearance.
|
|
(7) |
If the plastigage shows the clearance is still incorrect, try
the next larger or smaller bearing. Recheck the oil clearance.
If the proper clearance cannot be obtained by using the
appropriate larger or smaller bearings, replace the crankshaft
and start over.
|
If the marks are indecipherable because of an accumulation
of dirt and dust, do not scrub them with a wire brush or
scraper. Clean them only with solvent or detergent.
|
|
(8) |
Select the bearing by using the selection table.
Letters have been stamped on the side of block as a mark for
the size of each of the 5 main journal bores.
Use them, and the numbers or letters stamped on the crank (marks
for main journal size), to choose the correct bearings.
Crankshaft Main Bearing Selection
Table
Crankshaft main bearing
|
Cylinder block crankshaft journal bore mark
|
A
|
B
|
C
|
Crankshaft main journal mark
|
1
|
E (Red / Yellow)
|
D (Green)
|
C (None)
|
2
|
D (Green)
|
C (None)
|
B (Black)
|
3
|
C (None)
|
B (Black)
|
A (Blue)
|
Inspection Of Cylinder Block Crankshaft
Journal Bore
Mark
|
Cylinder block journal bore inner diameter
|
A or 1
|
52.000 - 52.006 mm
(2.0472 - 2.0475 in)
|
B or 2
|
52.006 - 52.012 mm
(2.0475 - 2.0477 in)
|
C or 3
|
52.012 - 52.018 mm
(2.0477 - 2.0479 in)
|
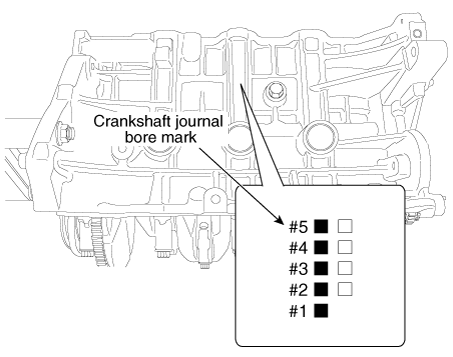
Inspection Of Crankshaft Main Journal
Mark
|
Crankshaft main journal outer diameter
|
1
|
47.954 - 47.960 mm
(1.8879 - 1.8882 in)
|
2
|
47.948 - 47.954 mm
(1.8877 - 1.8879 in)
|
3
|
47.942 - 47.948 mm
(1.8875 - 1.8877 in)
|
[Type A]
Top surface stamp
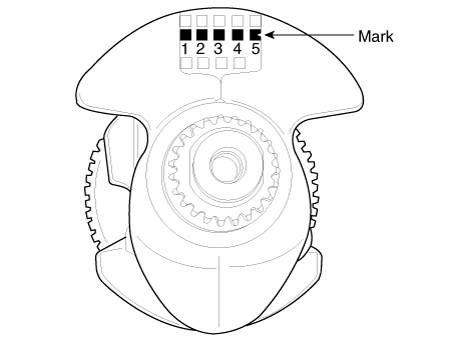
[Type B]
Bottom surface stamp
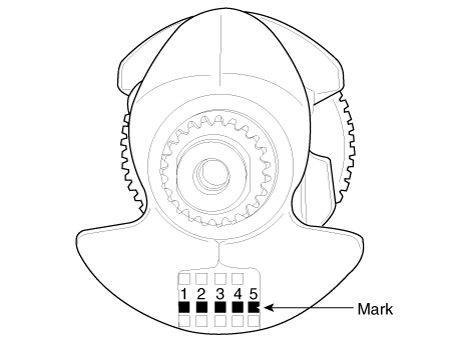
Inspection Of Crankshaft Main Bearing
Class
|
Color
|
Crankshaft main bearing thickness
|
A
|
Blue
|
2.026 - 2.029 mm
(0.0798 - 0.0799 in)
|
B
|
Black
|
2.023 - 2.026 mm
(0.0796 - 0.0798 in)
|
C
|
None
|
2.020 - 2.023 mm
(0.0795 - 0.0796 in)
|
D
|
Green
|
2.017 - 2.020 mm
(0.0794 - 0.0795 in)
|
E
|
Red / Yellow
|
2.014 - 2.017 mm
(0.0793 - 0.0794 in)
|
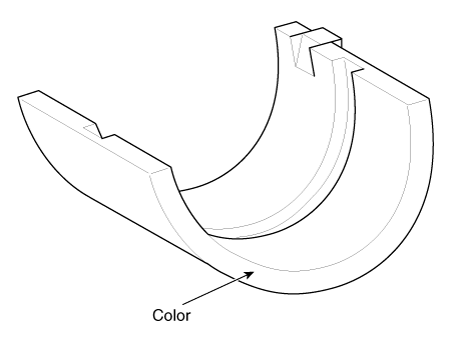
|
|